Enzyme Technology
High-fructose corn syrups (HFCS)
With the development of glucoamylase in the
1940s and 1950s it became a straightforward matter to produce high DE glucose
syrups. However, these have shortcomings as objects of commerce: D-glucose has
only about 70% of the sweetness of sucrose, on a weight basis, and is
comparatively insoluble. Batches of 97 DE glucose syrup at the final commercial
concentration (71% (w/w)) must be kept warm to prevent crystallisation or diluted
to concentrations that are microbiologically insecure. Fructose is 30% sweeter
than sucrose, on a weight basis, and twice as soluble as glucose at low
temperatures so a 50% conversion of glucose to fructose overcomes both problems
giving a stable syrup that is as sweet as a sucrose solution of the same
concentration (see Table 4.3). The isomerisation is possible by chemical
means but not economical, giving tiny yields and many by-products (e.g., 0.1 M
glucose 'isomerised' with 1.22 M KOH at 5°C under nitrogen for 3.5 months
gives a 5% yield of fructose but only 7% of the glucose remains unchanged, the
majority being converted to various hydroxy acids).
One of the triumphs of enzyme technology so
far has been the development of 'glucose isomerase'. Glucose is normally
isomerised to fructose during glycolysis but both sugars are phosphorylated. The
use of this phosphohexose isomerase may be ruled out as a commercial enzyme
because of the cost of the ATP needed to activate the glucose and because two
other enzymes (hexokinase and fructose-6-phosphatase) would be needed to
complete the conversion. Only an isomerase that would use underivatised glucose
as its substrate would be commercially useful but, until the late 1950s, the
existence of such an enzyme was not suspected. At about this time, enzymes were
found that catalyse the conversion of D-xylose to an equilibrium mixture of D-xylulose
and D-xylose in bacteria. When supplied with cobalt ions, these xylose
isomerases were found to isomerise a-D-glucopyranose to
a-D -fructofuranose
(see reaction scheme [1.5]), equilibration from the more abundant
b-D-glucopyranose
and to the major product b-D-fructopyranose occurring naturally and non-enzymically.
Now it is known that several genera of microbes, mainly bacteria, can produce
such glucose isomerases: The commercial enzymes are produced by Actinoplanes
missouriensis, Bacillus coagulans and various Streptomyces species; as they have
specificities for glucose and fructose which are not much different from that
for xylose and ways are being found to avoid the necessity of xylose as inducer,
these should perhaps now no longer be considered as xylose isomerases. They are
remarkably amenable enzymes in that they are resistant to thermal denaturation
and will act at very high substrate concentrations, which have the additional
benefit of substantially stabilising the enzymes at higher operational
temperatures. The vast majority of glucose isomerases are retained within the
cells that produce them but need not be separated and purified before use.
All glucose isomerases are used in
immobilised forms. Although differerent immobilisation methods have been used for
enzymes from differerent organisms, the principles of use are very similar.
Immobilisation is generally by cross-linking with glutaraldehyde, plus in some
cases a protein diluent, after cell lysis or homogenisation.
Originally, immobilised glucose isomerase was
used in a batch process. This proved to be costly as the relative reactivity of
fructose during the long residence times gave rise to significant by -product
production. Also, difficulties were encountered in the removal of the added Mg2+
and Co2+ and the recovery of the catalyst. Nowadays most isomerisation is
performed in PBRs (Table 5.2). They are used with high substrate concentration
(35-45% dry solids, 93-97% glucose) at 55-60°C. The pH is adjusted to 7.5-8.0 using sodium carbonate and magnesium sulphate is added to maintain enzyme
activity (Mg2+ and Co2+ are cofactors). The Ca2+ concentration of the glucose
feedstock is usually about 25 mm, left from previous processing, and this
presents a problem. Ca2+ competes successfully for the Mg2+ binding site on the
enzyme, causing inhibition. At this level the substrate stream is normally made
3 mM with respect to Mg2+. At higher concentrations of calcium a Mg2+ : Ca2+
ratio of 12 is recommended. Excess Mg2+ is uneconomic as it adds to the
purification as well as the isomerisation costs. The need for Co2+ has not been
eliminated altogether, but the immobilisation methods now used fix the cobalt
ions so that none needs to be added to the substrate streams.
Table 5.2. Comparison of glucose isomerisation
methods
Parameter
|
Batch
(soluble GI)
|
Batch
(immobilised Gl)
|
Continuous
(PBR)
|
Reactor volume (m3)
|
1100
|
1100
|
15
|
Enzyme
consumption (tonnes)
|
180
|
11
|
2
|
Activity, half-life (h)
|
30
|
300
|
1500
|
Active life,
half-lives
|
0.7
|
2
|
3
|
Residence time (h)
|
20
|
20
|
0.5
|
Co2+ (tonnes)
|
2
|
1
|
0
|
Mg2+ (tonnes)
|
40
|
40
|
7
|
Temperature (°C)
|
65
|
65
|
60
|
pH
|
6.8
|
6.8
|
7.6
|
Colour formation (A420)
|
0.7
|
0.2
|
< 0.1
|
Product refining
|
Filtration
C-treatment a
Cation exchange
Anion exchange
|
-
C-treatment
Cation exchange
Anion exchange
|
-
C -treatment
-
-
|
Capital, labour and
energy costs, £ tonne−1
|
5
|
5
|
1
|
Conversion cost, £
tonne−1
|
500
|
30
|
5
|
All processes start with 45% (w/w) glucose
syrup DE 97 and produce 10000 tonnes per month of 42% fructose dry syrup. Some
of the improvement that may be seen for PBR productivity is due to the
substantial development of this process.
a Treatment with activated carbon.
It is essential for efficient use of
immobilised glucose isomerase that the substrate solution is adequately purified
so that it is free of insoluble material and other impurities that might
inactivate the enzyme by chemical (inhibitory) or physical (pore-blocking)
means. In effect, this means that glucose produced by acid hydrolysis cannot be
used, as its low quality necessitates extensive and costly purification.
Insoluble material is removed by filtration, sometimes after treatment with
flocculants, and soluble materials are removed by ion exchange resins and
activated carbon beads. This done, there still remains the possibility of
inhibition due to oxidised by-products caused by molecular oxygen. This may be
removed by vacuum de-aeration of the substrate at the isomerisation temperature
or by the addition of low concentrations (< 50 ppm) of sulphite.
At equilibrium at 60°C about 51 % of the
glucose in the reaction mixture is converted to fructose (see Chapter 1 for a
full discussion of such reversible reactions). However, because of the excessive
time taken for equilibrium to be attained and the presence of oligosaccharides
in the substrate stream, most manufacturers adjust flow rates so as to produce
42-46% (w/w) fructose (leaving 47-51 % (w/w) glucose). To produce 100 tonnes
(dry substance) of 42% HFCS per day, an enzyme bed volume of about 4 m3 is
needed. Activity decreases, following a first-order decay equation. The
half-life of most enzyme preparations is between 50 and 100 days at 55°C.
Typically a batch of enzyme is discarded when the activity has fallen to an
eighth of the initial value (i.e., after three half -lives). To maintain a
constant fructose content in the product, the feed flow rate is adjusted
according to the enzyme activity. Several reactors containing enzyme
preparations of different ages are needed to maintain overall uniform production
by the plant (Figure 5.10). In its lifetime 1 kg of immobilised glucose
isomerase (exemplified by Novo's Sweetzyme T) will produce 10 -11 tonnes of 42%
fructose syrup (dry substance).
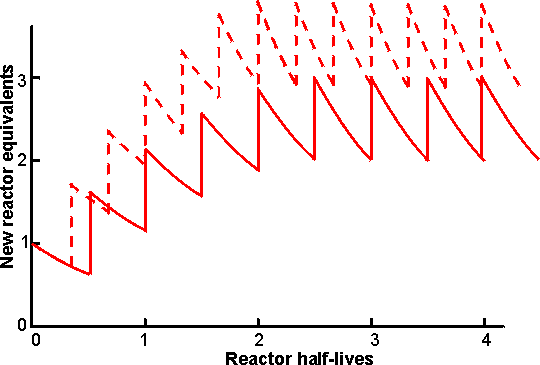
Figure 5.10. Diagram showing the production
rate of a seven-column PBR facility on start -up, assuming exponential decay of
reactor activity. The columns are brought into use one at a time. At any time a
maximum of six PBRs are operating in parallel, while the seventh, exhausted,
reactor is being refilled with fresh biocatalyst. ———
PBR activities allowed to
decay through three half-lives (to 12.5% initial activity) before replacement.
The final average productivity is 2.51 times the initial productivity of one
column. - - -- - - - PBR activities allowed to decay through two half-lives (to 25%
initial activity) before replacement. The final average productivity is 3.23
times the initial productivity of one column. It may be seen that the final
average production rate is higher when the PBRs are individually operated for
shorter periods but this 29% increase in productivity is achieved at a cost of
50% more enzyme, due to the more rapid replacement of the biocatalyst in the
PBRs. A shorter PBR operating time also results in a briefer start-up period
and a more uniform productivity.
After isomerisation, the pH of the syrup is
lowered to 4 - 5 and it is purified by ion-exchange chromatography and treatment
with activated carbon. Then, it is normally concentrated by evaporation to about
70% dry solids.
For many purposes a 42% fructose syrup is
perfectly satisfactory for use but it does not match the exacting criteria of
the quality soft drink manufacturers as a replacement for sucrose in acidic soft
drinks. For use in the better colas, 55% fructose is required. This is produced
by using vast chromatographic columns of zeolites or the calcium salts of cation
exchange resins to adsorb and separate the fructose from the other components.
The fractionation process, although basically very simple, is only economic if
run continuously. The fructose stream (90% (w/w) fructose, 9% glucose) is
blended with 42% fructose syrups to give the 55% fructose (42% glucose) product
required. The glucose-rich 'raffinate' stream may be recycled but if this is
done undesirable oligosaccharides build up in the system. Immobilised
glucoamylase is used in some plants to hydrolyse oligosaccharides in the
raffinate; here the substrate concentration is comparatively low (around 20% dry
solids) so the formation of isomaltose by the enzyme is insignificant.
Clearly the need for a second large fructose
enrichment plant in addition to the glucose isomerase plant is undesirable and
attention is being paid to means of producing 55% fructose syrups using only the
enzyme. The thermodynamics of the system favour fructose production at higher
temperatures and 55% fructose syrups could be produced directly if the enzyme
reactors were operated at around 95°C. The use of miscible organic co
-solvents may also produce the desired effect. Both these alternatives present a
more than considerable challenge to enzyme technology!
The present world market for HFCS is over 5
million tonnes of which about 60% is for 55% fructose syrup with most of the
remainder for 42% fructose syrup. This market is still expanding and ensures
that HFCS production is the major application for immobilised-enzyme
technology.
The high-fructose syrups can be used to
replace sucrose where sucrose is used in solution but they are inadequate to
replace crystalline sucrose. Another ambition of the corn syrup industry is to
produce sucrose from starch. This can be done using a combination of the enzymes
phosphorylase (EC 2.4.1.1), glucose isomerase and sucrose phosphorylase (EC
2.4.1.7), but the thermodynamics do not favour the conversion so means must be
found of removing sucrose from the system as soon as it is formed. This will not
be easy but is achievable if the commercial pull (i.e., money available) is
sufficient:
phosphorylase
starch (Gn) +
orthophosphate
starch (Gn-1) + a-glucose-1-phosphate
[5.1]
glucose isomerase
glucose
fructose [5.2]
sucrose
phosphorylase
a-glucose-1 -phosphate + fructose
sucrose + orthophosphate [5.3]
A further possible approach to producing
sucrose from glucose is to supply glucose at high concentrations to microbes
whose response to osmotic stress is to accumulate sucrose intracellularly.
Provided they are able to release sucrose without hydrolysis when the stress is
released, such microbes may be the basis of totally novel processes.
Home
| Back | Next
This page was established in 2004 and last updated by Martin
Chaplin on
6 August, 2014
|