Enzyme Technology
Continuous flow stirred tank reactors
This reactor consists of a well -stirred tank
containing the enzyme, which is normally immobilised. The substrate stream is
continuously pumped into the reactor at the same time as the product stream is
removed. If the reactor is behaving in an ideal manner, there is total
back-mixing and the product stream is identical with the liquid phase within the
reactor and invariant with respect to time. Some molecules of substrate may be
removed rapidly from the reactor, whereas others may remain for substantial
periods. The distribution of residence times for molecules in the substrate
stream is shown in Figure 5.4.
The CSTR is an easily constructed, versatile
and cheap reactor, which allows simple catalyst charging and replacement. Its
well -mixed nature permits straightforward control over the temperature and pH
of the reaction and the supply or removal of gases. CSTRs tend to be rather
large as the: need to be efficiently mixed. Their volumes are usually about five
to ten time the volume of the contained immobilised enzyme. This, however, has
the advantage that there is very little resistance to the flow of the substrate
stream, which may contain colloidal or insoluble substrates, so long as the
insoluble particles are not able to sweep the immobilised enzyme from the
reactor. The mechanical nature of the stirring limits the supports for the
immobilised enzymes to materials which do not easily disintegrate to give 'fines' which may enter the product stream. However, fairly small particle (down
to about 10 mm diameter) may be used, if they are sufficiently dense to stay
within the reactor. This minimises problems due to diffusional resistance.
An ideal CSTR has complete back -mixing
resulting in a minimisation of the substrate concentration, and a maximisation
of the product concentration, relative to the final conversion, at every point
within the reactor the effectiveness factor being uniform throughout. Thus,
CSTRs are the preferred reactors, everything else being equal, for processes
involving substrate inhibition or product activation. They are also useful where
the substrate stream contains an enzyme inhibitor, as it is diluted within the
reactor. This effect is most noticeable if the inhibitor concentration is
greater than the inhibition constant and [S]0/Km is low for competitive
inhibition or high for uncompetitive inhibition, when the inhibitor dilution has
more effect than the substrate dilution. Deviations from ideal CSTR behaviour
occur when there is a less effective mixing regime and may generally be overcome
by increasing the stirrer speed, decreasing the solution viscosity or
biocatalyst concentration or by more effective reactor baffling.
The rate of reaction within a CSTR can be
derived from a simple mass balance to be the flow rate (F) times the difference
in substrate concentration between the reactor inlet and outlet. Hence:
(5.7)
Therefore:
(5.8)
from equation (5.4):
(5.9)
Therefore:
(5.10)
This equation should be compared with that
for the PBR (equation (5.6)). Together these equations can be used for comparing
the productivities of the two reactors (Figures 5.5 and 5.6).
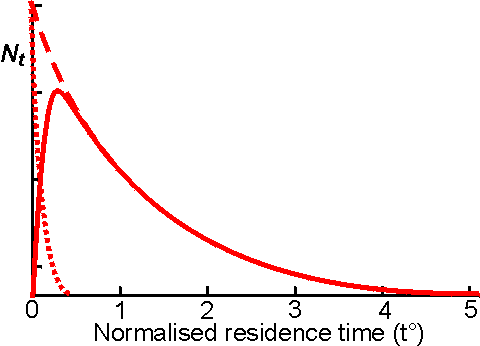
Figure 5.4. The residence time distribution
of a CSTR. The relative number of molecules resident within the reactor for a
particular time N, is plotted against the normalised residence time (i.e., tF/V,
where V is the reactor volume, and F is the flow rate; it is the time relative
to that required for one reactor volume to pass through the reactor). The
residence time distribution of non -reacting media molecules ( ----------- which
obeys the relationship
, where [M] is the
concentration of media molecules, giving a half-life for remaining in the
reactor of, product (———
) and substrate (·········)
are shown. The reaction S
P is assumed, and substrate molecules that have long
residence times are converted into product, the average residence time of the
product being greater than that for the substrate. The composition of the
product stream is identical with that of the liquid phase within the reactor.
This composition may be calculated from the relative areas under the curves and,
in this case, represents a 90% conversion. Under continuous operating conditions
(operating time > 4V/F), the mean residence time within the reactor is V/F.
However, it may be noted from the graph that only a few molecules have a
residence time close to this value (only 7% between 0.9V/F and 1.1 V/F) whereas
20% of the molecules have residence times of less than 0.1 V/F or greater than
2.3V/F. It should be noted that 100% of the molecules in an equivalent ideal PBR
might be expected to have residence times equal to their mean residence time.
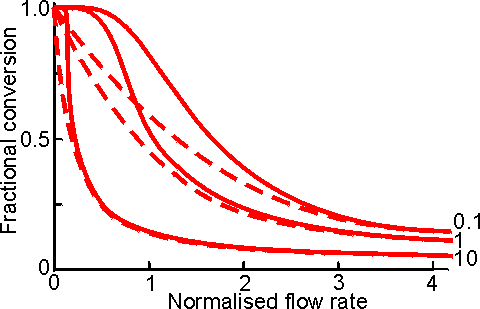
Figure 5.5. Comparison of the changes in
fractional conversion with flow rate between the PBR (———) and CSTR (-----------) at
different values of [S]0/Km (10,1 and 0.1, higher [S]0/Km giving the higher
curves). The flow rate is normalised with respect to the reactor's volumetric
enzyme content ( = FKm/Vmax. It can be seen that there is little
difference between the two reactors at faster flow rates and lower conversions,
especially at high values of [S]0/Km.
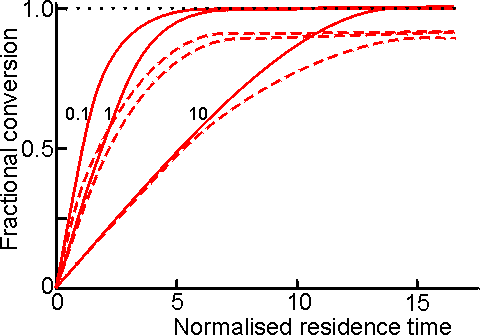
Figure 5.6. Comparison of the changes in
fractional conversion with residence time between the PBR (———) and CSTR (-----------) at different values of [S]0/Km (10, 1 and 0.1; higher [S]0/Km values giving
the lower curves). The residence time is the reciprocal of the normalised flow
rate (see Figure 5.5). If the flow rate is unchanged then the 'normalised
residence time' may be thought of as the reactor volume needed to produce the
required degree of conversion.
Equations describing the behaviour of CSTRs
and PBRs utilising reversible reactions or undergoing product or substrate
inhibition can be derived in a similar manner, using equations (1.68),
(1.85)
and (1.96) rather than (1.8):
Substrate -inhibited PBR:
(5.11)
Substrate -inhibited CSTR:
(5.12)
Product -inhibited PBR:
(5.13)
Product -inhibited CSTR:
(5.14)
Reversible reaction in a PBR:
(5.15)
Reversible reaction in a CSTR:
(5.16)
X in equations (5.15) and (5.16) is the
fractional conversion for a reversible reaction.
(5.17)
The meaning of other symbols used in
equations (5.11)-(5.17) are given Chapter 1. These equations may be used to
compare the size of PBR and CSTR necessary to achieve the same conversion under
various conditions (Figure 5.7). Another useful parameter for comparing these
reactors is the productivity. This can be derived for each reactor assuming a
first-order inactivation of the enzyme (equation (1.26)). Combined with
equation (5.6) for PBR, or (5.10) for CSTR, the following relationships are
obtained on integration:
PBR:
(5.18)
CSTR:
(5.19)
where kd is the first -order inactivation
constant (i.e., kd1, in equation (1.25)) and the fractional conversion subscripts
refer to time = 0 or t. The change in productivity (Figure 5.8) and fractional
conversion (Figure 5.9) of these reactors with time can be compared using these
equations.
These reactors may be operated for
considerably longer periods than that determined by the inactivation of their
contained immobilised enzyme, particularly if they are capable of high
conversion at low substrate concentrations (Figure 5.9). This is independent of
any enzyme stabilisation and is simply due to such reactors initially containing
large amounts of redundant enzyme.
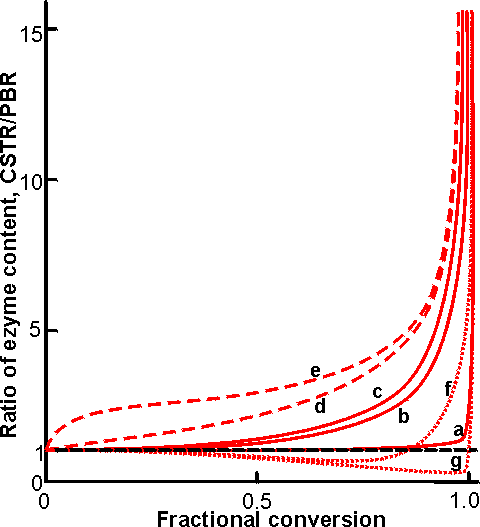
Figure 5.7. Comparison of the ratio, of the
enzyme content in a CSTR to that in a PBR, necessary to achieve various degrees
of conversion for a range of process conditions. The actual size of the CSTR
will be five to ten times greater than indicated due to the necessity of
maintaining stirring within the vessel. ———Uninhibited reaction;
············ product
inhibited; ---------substrate inhibited. (curve a) [S]0/Km = 100; (curve b)
[S]0/Km = 1; (curve c) [S]0/Km < 0.01; (curve d)
[S]0/Km = 1, product
inhibited KP/Km = 0.1; (curve e) [S]0/Km = 1, product inhibited
KP/Km =
0.01; (curve f) [S]0/Km = 1, substrate inhibited [S]0/KS =
10; (curve g) [S]0/Km = 100; substrate inhibited [S]0/KS = 10. The size of a CSTR becomes
prohibitively large at high conversions (e.g., using curve b, a CSTR contains
three times the enzyme in a PBR to achieve a 90% conversion, but this increases
to 18 times for 99% conversion. The difference between the two types of reactor
is increased if the effectiveness factor (h) is less than one due to diffusional
effects.
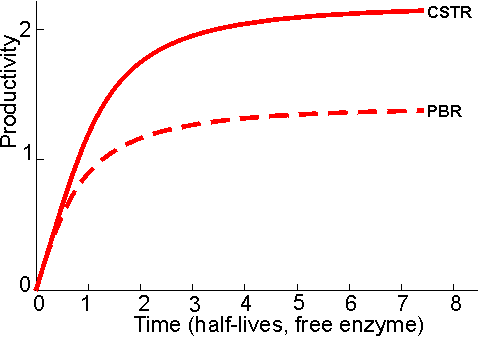
Figure 5.8. The
change in productivity of a PBR (---------)
and CSTR (———) with time, assuming an initial
fractional conversion (X0) = 0.99 and [S]0/Km
= 100. The units of time are half -lives of the free enzyme ( )
and the productivity is given in terms of (FXt1/2). Although the
overall productivity is 1.6 times greater for a CSTR than a PBR, it should be
noted that the CSTR contains 1.9 times more enzyme.
In general, there is little or no back
-pressure to increased flow rate through the CSTR. Such reactors may be started
up as batch reactors until the required degree of conversion is reached, when
the process may be made continuous. CSTRs are not generally used in processes
involving high conversions but a train of CSTRs may approach the PBR
performance. This train may be a number (greater than three) of reactors
connected in series or a single vessel divided into compartments, in order to
minimise back-mixing CSTRs may be used with soluble rather than immobilised
enzyme if an ultrafiltration membrane is used to separate the reactor output
stream from the reactor contents. This causes a number of process difficulties,
including concentration polarization or inactivation of the enzyme on the
membrane but may be preferable in order to achieve a combined reaction and
separation process or where a suitable immobilised enzyme is not readily
available.
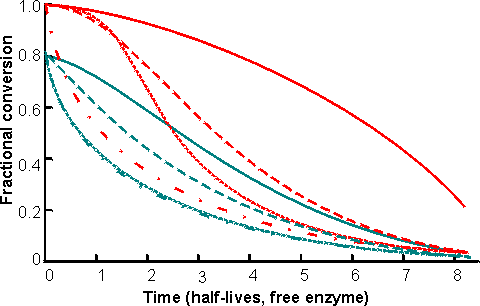
Figure 5.9.
The change in fractional conversion of PBRs and CSTRs with time, assuming initial
fractional conversion (X0) of 0.99
or 0.80. ————CSTR,
[S]o/Km = 0.01; -
- - - - - CSTR, [S]0/Km
= 100; ············
PBR [S]0/Km = 0.01; ·-·-·-·-·-·-·-·
PBR [S]0/Km = 100. The time is given in terms
of the half -life of the free enzyme ( ).
Although the CSTR maintains its fractional conversion for a longer period than
the PBR, particularly at high X0. It should be noted that a CSTR
capable of X0 = 0.99 at a substrate feed concentration of [S]0/Km
= 0.01 contains 22 times more enzyme than an equivalent PBR, but yields only
2.2 times more product. The initial stability in the fractional conversion over
a considerable period of time, due to the enzyme redundancy, should not be confused
with any effect due to stabilisation of the immobilised enzyme.
Home
| Back | Next
This page was established in 2004 and last updated by Martin
Chaplin on
6 August, 2014
|